Comprehensive Guide: What is Porosity in Welding and Just How to avoid It
Comprehending Porosity in Welding: Exploring Causes, Results, and Avoidance Strategies
As specialists in the welding market are well conscious, recognizing the causes, results, and prevention methods connected to porosity is crucial for accomplishing robust and reliable welds. By delving into the origin creates of porosity, analyzing its destructive impacts on weld top quality, and discovering reliable avoidance strategies, welders can boost their expertise and abilities to generate high-quality welds regularly.
Typical Reasons of Porosity
Contamination, in the type of dust, grease, or rust on the welding surface area, produces gas pockets when heated, leading to porosity in the weld. Incorrect shielding occurs when the shielding gas, frequently used in processes like MIG and TIG welding, is unable to fully protect the molten weld swimming pool from reacting with the bordering air, resulting in gas entrapment and succeeding porosity. Additionally, insufficient gas insurance coverage, frequently due to inaccurate circulation prices or nozzle positioning, can leave components of the weld unguarded, enabling porosity to create.
Results on Weld Quality
The existence of porosity in a weld can significantly jeopardize the general high quality and stability of the bonded joint. Porosity within a weld develops spaces or cavities that damage the framework, making it more vulnerable to splitting, deterioration, and mechanical failure. These gaps work as stress concentrators, decreasing the load-bearing capability of the weld and boosting the likelihood of early failing under applied stress. Additionally, porosity can likewise offer as prospective sites for hydrogen entrapment, more worsening the deterioration of the weld's mechanical residential properties.
In addition, porosity can impede the performance of non-destructive screening (NDT) strategies, making it testing to find various other issues or discontinuities within the weld. This can bring about considerable safety concerns, particularly in essential applications where the structural honesty of the welded parts is vital.
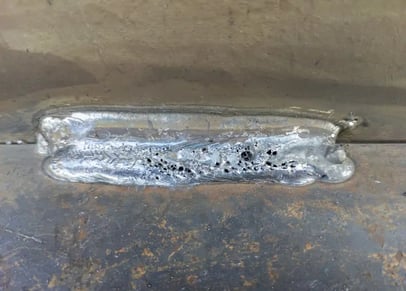
Prevention Techniques Summary
Offered the detrimental influence of porosity on weld quality, efficient prevention methods are essential to preserving the structural stability of visit this page bonded joints. In addition, choosing the proper welding criteria, such as voltage, existing, and travel speed, can aid decrease the risk of porosity formation. By integrating these prevention methods right into welding practices, the event of porosity can be substantially reduced, leading to more powerful and a lot more trusted welded joints.
Significance of Proper Protecting
Proper shielding in welding plays a vital function in protecting against climatic contamination and guaranteeing the integrity of bonded joints. Protecting gases, such as argon, helium, or a combination of both, are frequently utilized to shield the weld swimming pool from reacting with components airborne like oxygen and nitrogen. When these reactive components come right into contact with the warm weld pool, they can trigger porosity, bring about weak welds with decreased mechanical residential or commercial properties.
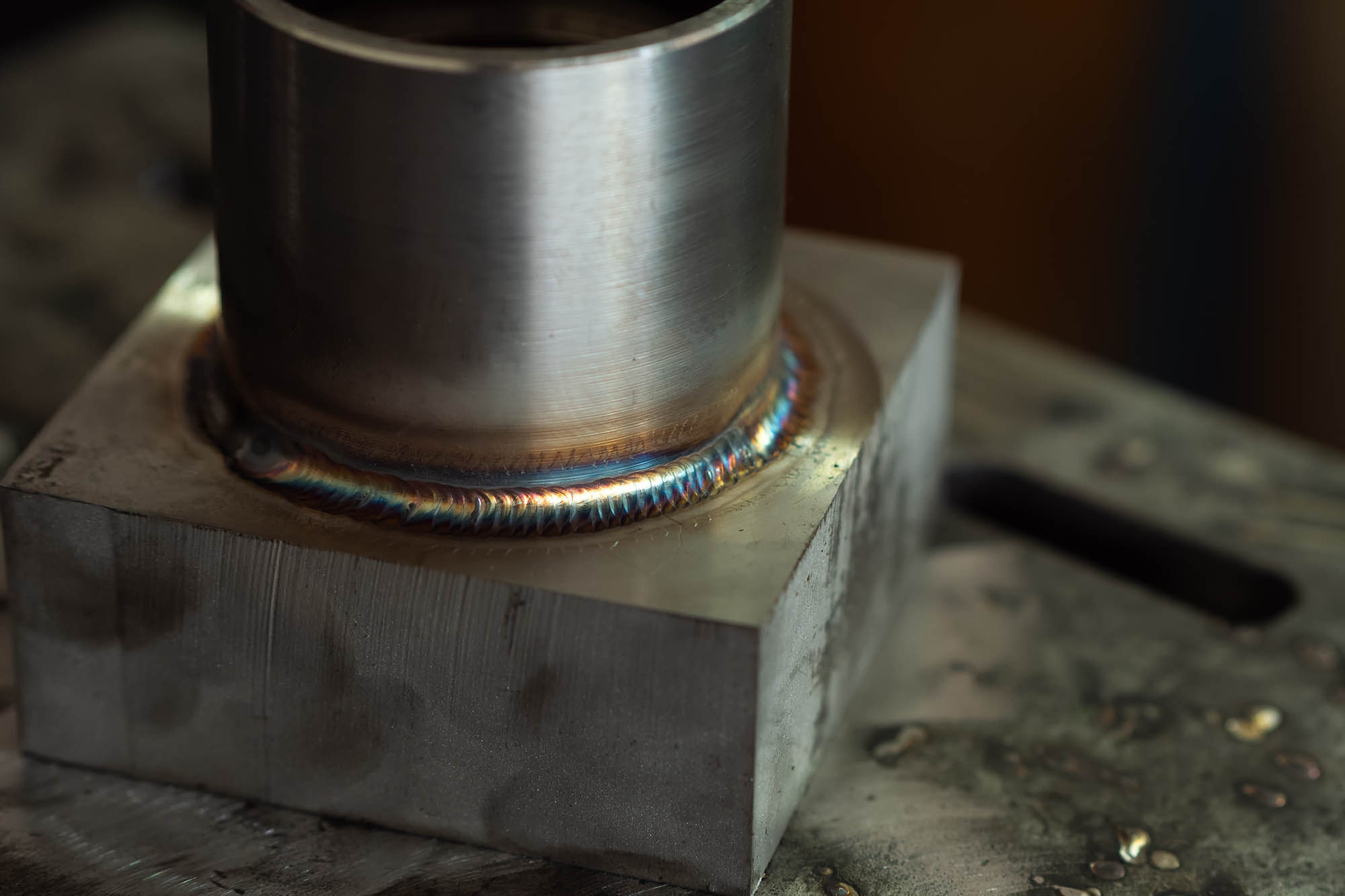
Poor shielding can cause various issues like porosity, spatter, and oxidation, endangering the structural stability of the welded joint. Sticking to proper securing practices is vital to produce top notch welds with marginal flaws and guarantee the durability and reliability of the bonded parts.
Tracking and Control Techniques
How can welders effectively check and control the welding procedure to make certain optimum results and prevent issues like porosity? By continually monitoring these variables, welders can identify discrepancies from the excellent conditions and make instant changes to his explanation stop porosity formation.

In addition, implementing correct training programs for welders is important for keeping track of and regulating the welding procedure successfully. What is Porosity. Informing welders on the significance of keeping consistent parameters, such as appropriate gas shielding and take a trip speed, can assist prevent porosity concerns. Regular analyses and accreditations can also guarantee that welders are proficient in tracking and controlling welding processes
Furthermore, the usage of automated welding systems can enhance surveillance and control abilities. These systems can precisely manage welding specifications, reducing the probability of human error and making sure constant weld helpful site top quality. By combining advanced monitoring modern technologies, training programs, and automated systems, welders can efficiently check and control the welding process to decrease porosity issues and achieve high-quality welds.
Conclusion
